Cobot safety classification: are they really as “safe” as you think?
Collaborative robots, or cobots, are increasingly hailed as the future of industrial automation. They're said to be safe, flexible, and easy to integrate alongside human coworkers. But are all these assumptions actually true? Isn’t the term “safe” being thrown around a little too loosely?
In this blog, we break away from the standard narrative. We'll take a deeper look at cobot safety classifications and why they matter more than you might think.
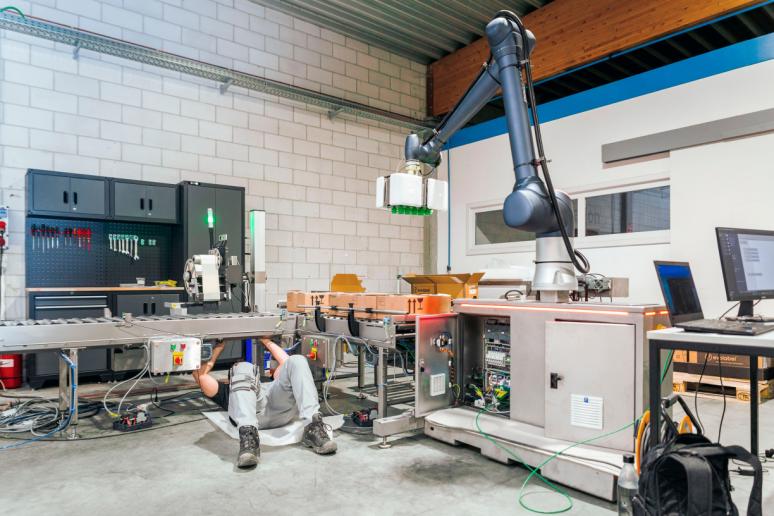
Safety classification: It’s not the robot, it’s the application that defines the risk
One of the most common misconceptions is that cobots fall into a single, fixed safety class. In reality, it’s the application that determines the safety level, not the robot itself.
A cobot might safely operate without fencing in one facility, yet require full guarding in another. Why? Because the task, tooling, environment, and speed vary from one setup to another.
Example: Imagine you have a cobot that assembles components on a production line. If it's simply snapping plastic clips into place at low speed, a risk assessment might conclude that no physical guarding is required. But give that same cobot a screwdriver and high-torque tool settings, and suddenly, you’re dealing with a much riskier situation.
So no, there’s no such thing as a universally safe cobot. Everything depends on the application and a thorough environmental analysis.
CE certification vs. workplace safety
Another common trap: thinking that a CE-certified cobot is automatically safe for your specific workplace.
Manufacturers supply cobots with a CE mark, which means the device itself complies with EU directives. But that certification does not apply to your specific integration. As soon as you attach a gripper, change the software, or modify the process, the situation changes and a new risk assessment is required.
That’s why collaboration is key. At Promation, we support our clients with much more than installation. We assist with:
- Tailored risk assessments
- Machine safety documentation
- Integration of sensors and safety systems
- Operator and maintenance training
Safety isn’t a plug-and-play feature. It’s a continuous process, to be considered, tested, and refined.
What do the standards say?
The ISO/TS 15066 standard focuses specifically on collaborative robots. It defines limits for force and pressure that cobots can apply when in contact with humans. But again, context matters. These limits are based on lab tests and average scenarios. Every real-world application still requires a case-specific risk analysis.
And don’t Final thoughts: Look beyond the brochurebe fooled, these thresholds are often higher than expected. A cobot operating “within the norm” can still cause pain or discomfort upon collision.
Bottom line: Standards are helpful, but they don’t guarantee complete safety.
Smart sensors make the difference
At Promation, we believe safety and efficiency go hand in hand. That’s why we integrate intelligent sensor technologies, such as:
- 3D cameras to continuously scan the environment and detect motion
- Force sensors in grippers to measure and adapt applied pressure
- Zone monitoring with light curtains or laser scanners
This enables our cobots to respond in real time, making human-robot collaboration safer and more intuitive than ever. But again: there’s no one-size-fits-all sensor. The right choice depends on your specific environment and application.
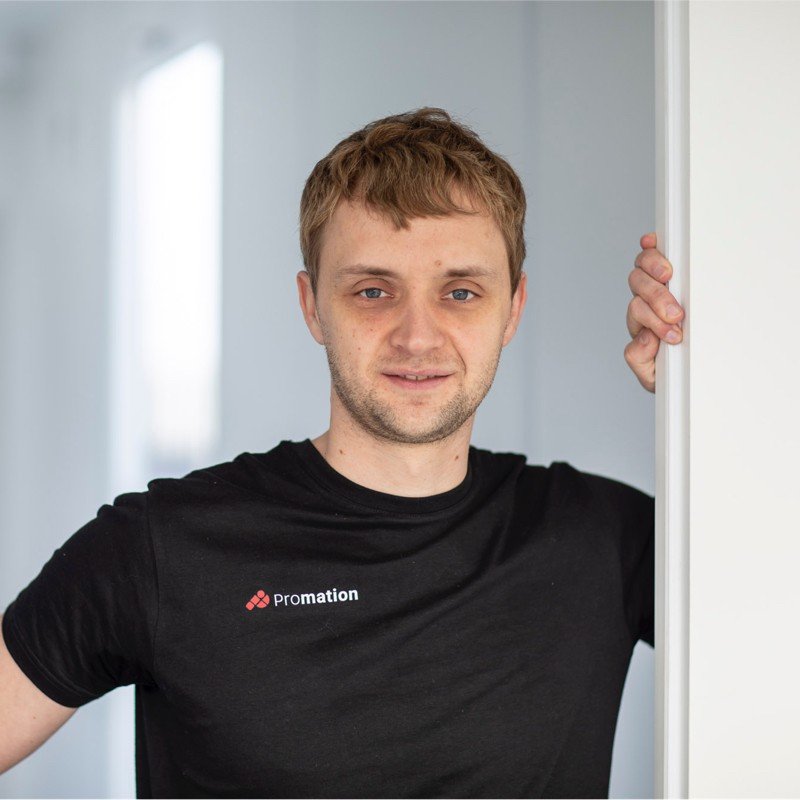
Written by Stijn Provoost
Founder of Promation. Passionate about programming and new technologies. With Promation, Stijn has one major goal: to improve production processes through industrial automation, robotics, and vision systems.
Final thoughts: look beyond the brochure
Cobots are a fantastic innovation, when used wisely. Don’t blindly rely on “safe” as a buzzword. Instead, take a critical look at your setup. At Promation, we go far beyond delivery. We ask the right questions, co-create tailored solutions, and help you build a system that’s truly safe, reliable, and future-proof.